Description
The SPH is a self-contained or “portable” compactor that is specifically designed for waste streams that contain a large percentage of wet waste. The self-contained compactor will contain all of the waste stream liquids in the unitized container and prevent/eliminate seepage. Each compactor is manufactured with fully welded seams, contains a 4″ liquid sump area and is equipped with a dump door that contains a full perimeter flexible “T-seal”. This seal prevents any migration of liquids between the container door frame and the door itself. This model is available in a wide range of capacities from 15 to 34 cubic yards and can be customized to fit our clients individual needs. This model has one unique advantage over the standard SPH-X or SPH-XWM compactors. It can be equipped with a 6″ diameter cylinder; which enables it to produce greater compaction forces and generate larger payloads.
Technical Details
Standard Features
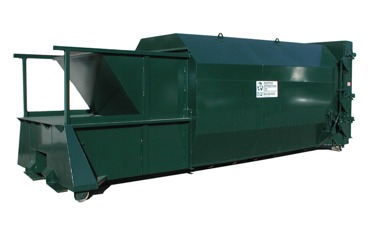
- UL/CSA Approved Design
- Meets/exceeds ANSI Z245.2 regulations
- Meets/exceeds OSHA regulations
- PLC “flex-design” based control systems
- NEMA 4 rated enclosure
- Internal timers prevent system run-on
- Self-diagnostic indicators
- 24-volt controls
- Adjustable multi-cycle timer
- 75% and 100% full light
- Auto-alert maintenance mode
- Heavy duty oil-tight pushbutton controls
- Key lockable start pushbutton
Mechanical Specifications
SPH28 | SPH30 | SPH32 | |
---|---|---|---|
Charge Chamber Volume | 1.73 cu yd | 1.73 cu yd | 1.73 cu yd |
Charge Chamber Opening Size | 42″ x 60″ | 42″ x 60″ | 42″ x 60″ |
Ram Face Size | 24″ x 60″ | 24″ x 60″ | 24″ x 60″ |
Ram Penetration | 6″ | 6″ | 6″ |
Compaction Force Normal | 39,250 lbs | 39,250 lbs | 39,250 lbs |
Compaction Force Maximum | 43,175 lbs | 43,175 lbs | 43,175 lbs |
Cycle Time | 47 seconds | 47 seconds | 47 seconds |
System Pressure Normal | 2000 psi | 2000 psi | 2000 psi |
System Pressure Maximum | 2200 psi | 2200 psi | 2200 psi |
Pump Capacity | 10 gpm | 10 gpm | 10 gpm |
Motor Size | 10 hp | 10 hp | 10 hp |
Cylinder Size | 2 x 5″0 | 2 x 5″0 | 2 x 5″0 |
Cylinder Type | Double Acting | Double Acting | Double Acting |
Ram Face Pressure Normal | 23.4 psi | 23.4 psi | 23.4 psi |
Ram Face Pressure Maximum | 25.7 psi | 25.7 psi | 25.7 psi |
Oil Tank Capacity | 30 gal | 30 gal | 30 gal |
Shipping Weight (Head only) | 9,860 lbs | 10,050 lbs | 10,460 lbs |
Electrical Specifications
Control System | 110 volt 60 cycle powered by step-down transformer |
Control Panel | Fully wired. Keyed start button, emergency stop, full lights, reset button, PLC, dual current sensors |
Power | 208/230/575 Volt, 3 Phase 60 Cycle |
Dimensions
A | B | C | D | E | F | |
---|---|---|---|---|---|---|
SPH28 | 264″ | 102″ | 102″ | 45″ | 42″ | 60″ |
SPH30 | 276″ | 102″ | 102″ | 45″ | 42″ | 60″ |
SPH32 | 306″ | 102″ | 102″ | 45″ | 42″ | 60″ |
Optional Equipment
- Advance-warning light
- Fluid-filled pressure gauge
- Oil heater
- Odour control system
- Open hopper (for top or loading dock)
- Fully enclosed hopper with door
- Through the wall installation kits
- Walk-on or drive-on decks
- Safety gate
- Hydraulic cart-dump systems
Electrical system upgrades
- System monitor: SCADA panel (add-on panel or integrated upgrade) provides cell-based monitoring of all systems including container fullness, safety circuit devices, container positioning, hydraulic system devices including reservoir fullness, oil temperature and system in-use time
- Remote start/stop station
- Auto-start system (photo-eye or sonic sensor)
- Wireless remote control
- Biometric interface
- HMI based operator interface for tie into building monitoring systems
Hydraulic system upgrades
- Single phase and three phase power units
- Hi-lo hydraulic pumps for reduced cycle time applications
- Regen circuit for improved hydraulic fluid circulation
- Over-sized oil reservoirs to accommodate ancillary devices and improved heat sink
- Oil cooler for high duty cycle applications
- Bio-degradable oil
- In tank oil heater
- Sonic sensors for oil fullness monitoring
- Low temperature oil (as low as -60 Celsius is available)
Compactor upgrades
- Custom chute systems
- Custom weather enclosures
- Drive-on deck systems (certified up to 20,000 lbs.)
- Tongue and grooved floor designs
- AR plate floors and sides for reduced press head/compactor shell wear
- Pad-less set-up for installation on asphalt
- Custom hydraulic cart tipping systems
- Light curtain-based safety sensors
- Custom steel safety barriers
- Custom hydraulic lift systems